FDCA and plantMEG™ together make a 100% plant-based plastic PEF

PEF
PEF is a 100% plant-based, recyclable polymer with a wide range of applications such as packaging, textiles, film, and many more. PEF has a powerful combination of environmental features and superior functionality. It shows improved barrier properties for carbon dioxide (CO2) and oxygen, leading to a longer shelf life of packaged products. It also offers higher mechanical strength, which means that thinner PEF packaging can be produced and fewer resources are required. In combination with the plant-based feedstock, these added functionalities give PEF all the attributes required to become the next-generation polyester.
Superior barrier properties:
- PEF’s oxygen barrier is 10 times better than PET
- PEF’s CO2 barrier is 6 to 10 times better than PET
- PEF’s water barrier is twice as good as PET’s
More attractive thermal properties:
- The Tg (glass transition temperature) of PEF is 86°C compared to the Tg of PET of 74°C
- The Tm (melting point) of PEF is 235°C compared to the Tm of PET of 265°C
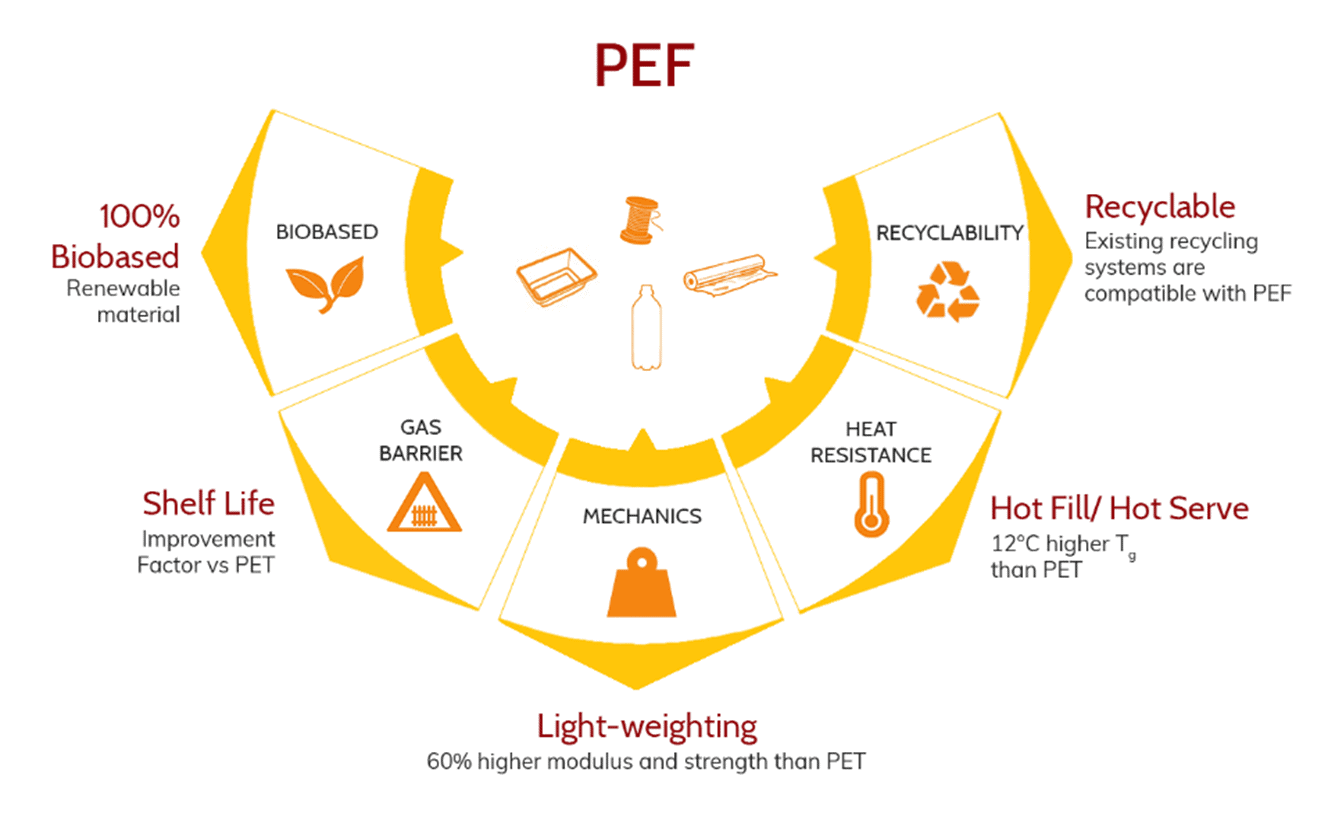
Addressing the need for a circular new plastics economy
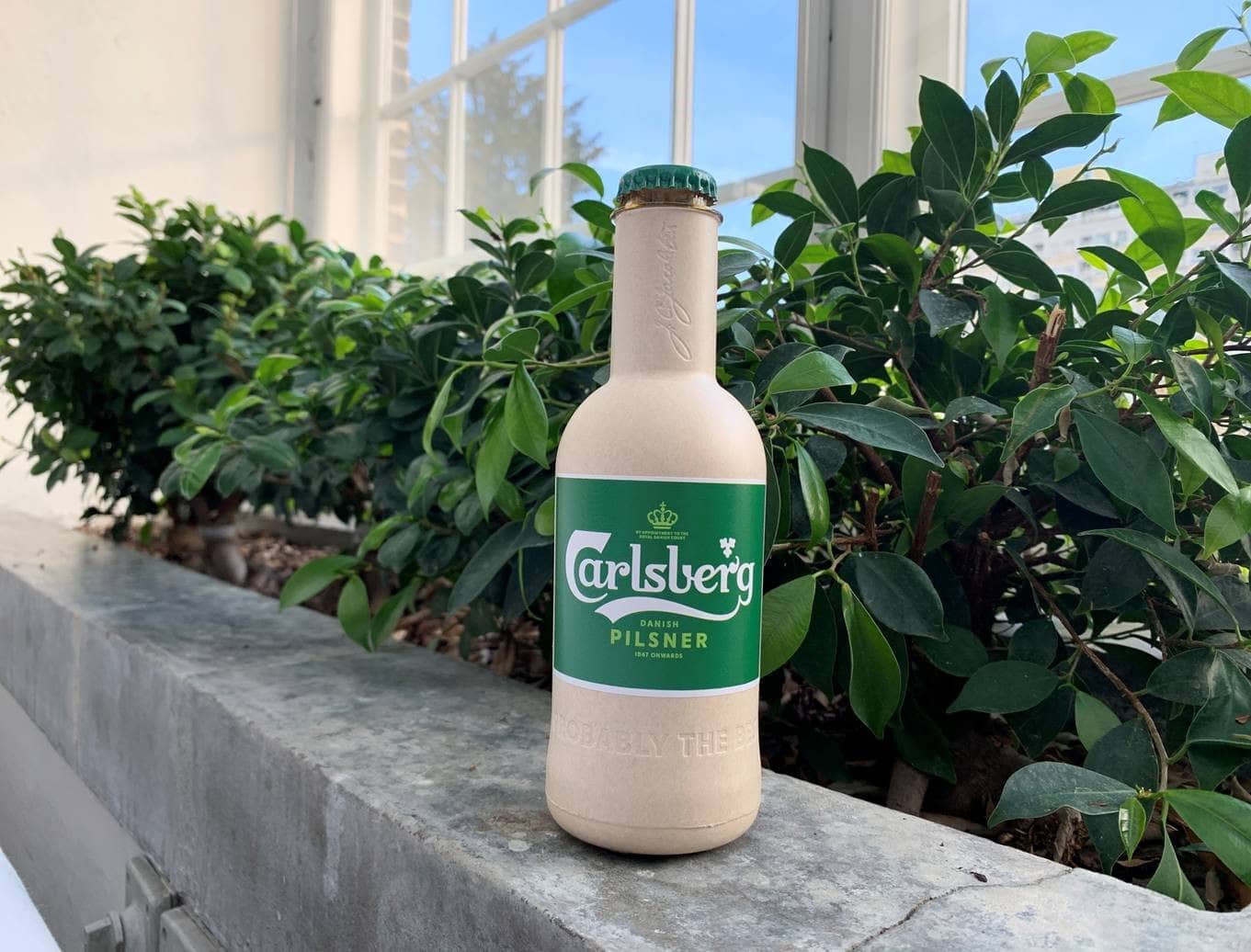
Reuse: Performance potential PEF in reuse under development
Recycle: PEF has a proven fit with existing sorting and recycling facilities and can substitute barrier materials and coatings in multi-layer packaging solutions which currently are challenging to recycle

High-value applications
PEF bottles
- Lower carbon footprint
- Circular: recyclable alternative to non-recyclable packaging formats
- Longer shelf life for fresh products, beer, etc
- Visually attractive bottles
- Monolayer PEF and combination with other materials possible
- Competing materials: glass, aluminum, paper, PET and multi-layer bottles
- Volume: 100 million ton/year
PEF fibers
- Lower carbon footprint
- Circular: recyclable alternative to non-recyclable packaging formats
- Stronger properties
- Textiles, upholstery, car tires, industrial fibers
- Competing materials: PET, nylon, cotton
- Volume: >50 million ton/year

PEF film and other applications
- Lower carbon footprint
- Circular: recyclable alternative to non-recyclable packaging formats
- Longer shelf life for fresh products
- Markets: packaging of food and non-food products
- Competing materials: glass, aluminum, paper, PET and multi-layer
- Volume: >5 million ton per year
FDCA
The main building block for PEF is furandicarboxylic acid (FDCA). Given the huge potential of FDCA, industrial production of this building block has been pursued and researched for over 100 years, without success. As such, FDCA has been called ‘the sleeping giant’. Avantium believes that our YXY® Technology can finally unlock the full potential of FDCA. The FDCA monomer offers exciting opportunities to create a wide range of polymers. These include polyesters, polyamides and polyurethanes, as well as coating resins, plasticizers and other chemical products.
plantMEG™
PlantMEG™ is an important chemical building block for PET or PEF resin for bottles and packaging; fibers for apparel, furniture and automotive; and solvents (e.g. paint and coatings) and coolants.
The use of plantMEG™ will provide brands with a sustainable, recyclable, and innovative ingredient capable of attracting environmentally conscious consumers
Favorable global MEG market dynamics
Projected to grow from 28 million tonnes to 50 million tonnes by 2040. The compound annual
growth rate between 2005 and 2022 was 4.8%
Impact
Up to 83% CO2 reduction compared to fossil-MEG and independent from fossil feedstock
Cost-competitive
Best-in-class single step catalytic process making plantMEG™ cost competitive with chemical equivalence
Scalable
Demonstration plant opened in 2019 with a clear path to scale-up and commercialisation
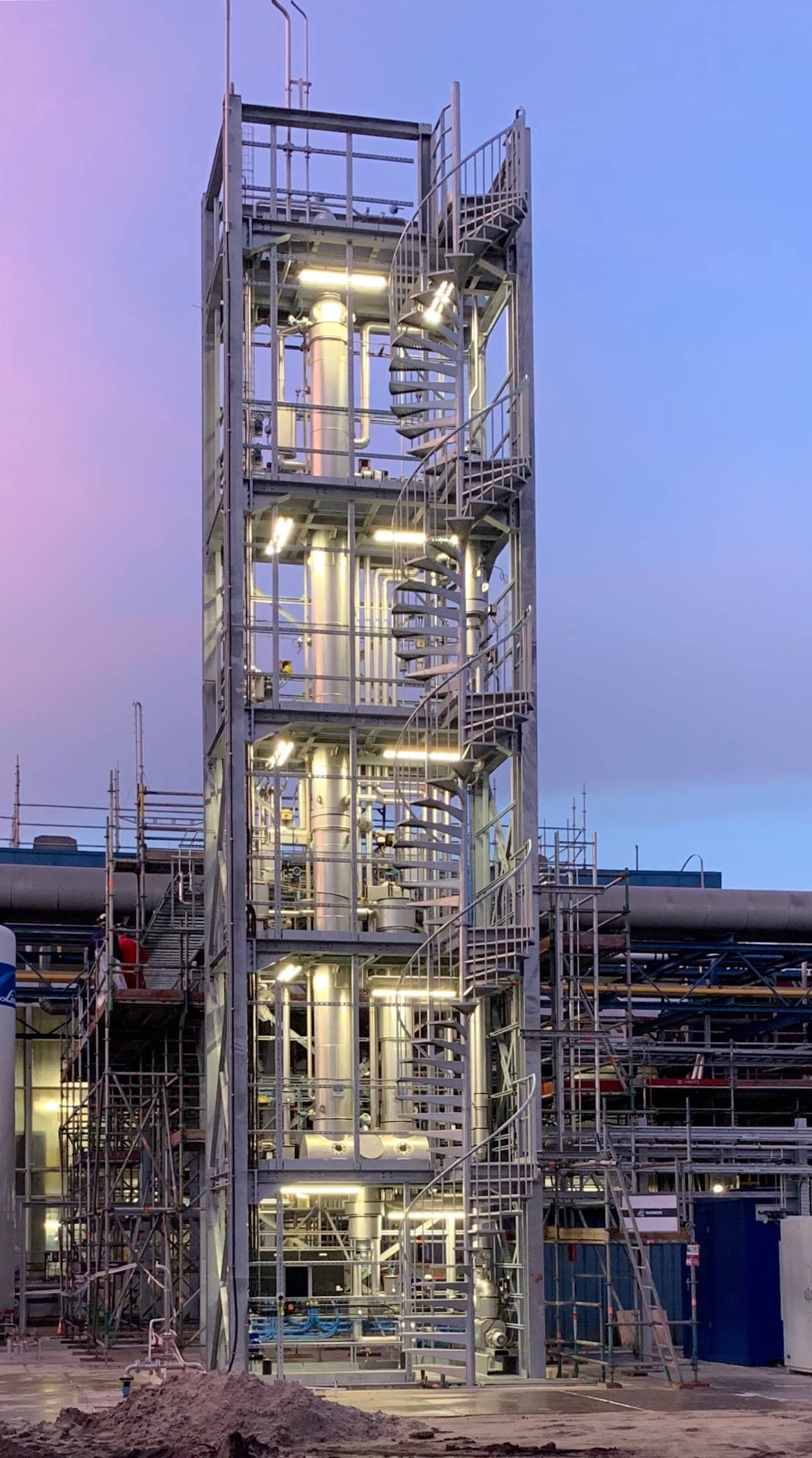